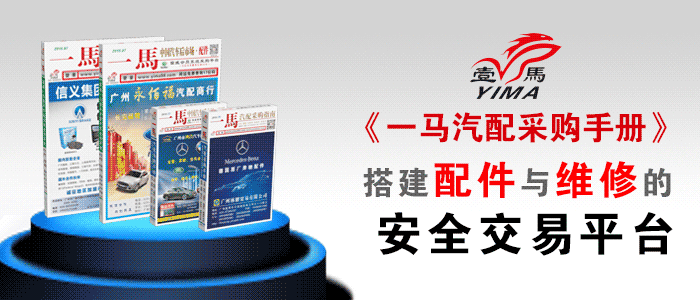

随着汽车工业的发展,模块化已成为汽车大规模生产的趋势。自上世纪90年代末以来,大众、丰田、通用汽车都启用了模块化生产方式。中国汽车要实现《中国制造2025》规划,也需要发展模块化制造。
目前,很多中国汽车企业都遇到了成长的“烦恼”,新产品创新、地域扩张、分销渠道拓展等都增加了经营的复杂 度,导致整体成本上升。以某知名卡车制造商为例,该企业拥有4个不同的品牌,共有150款车型和4000多个产品版本,这还不包括客户订制产品。好在已有 本土汽车企业意识到降低复杂度和模块化的重要性,有的企业已开始行动,但并没有确定合适的方法。
事实上,模块化的具体方法各不相同。大众汽车首先实施了覆盖旗下所有品牌的平台理念,丰田应用了零部件标准 化,通用汽车对不同车型的版本数量进行了控制。在卡车行业,戴姆勒对旗下所有品牌的部分车型实施了全球标准,而斯堪尼亚提供了一系列标准化的卡车元件供客 户选择。同时,这些方法也是搭配使用的,如大众同时应用了标准化模块和模块化平台(MQB)方法,丰田和通用汽车也都使用了全球平台。由此可见,模块化管 理并没有全球统一的解决方案,企业必须根据自身战略和市场渠道制定适合自己的管理方法。
专家团队需定期将模块化进程和待解决问题报告给高管,报告内容主要包括衡量业绩的关键参数,例如被淘汰的版本数量、预期的成本节约水平和当前的问题及挑战。提前确定报告结构,有利于企业专注于关键问题并高效地制定管理决策,维持专家团队的运行。
因此,建立全球模块架构,需涉及所有产品线和品牌的发展及周期规划。模块周期计划与车辆周期计划相关,模块供 应商应尽早参与讨论和更新,以利于确定整合新技术和模块工艺的最佳实践方案。笔者认为,中国整车企业在采用模块化生产方式时,在借鉴跨国车企成功的方法和 实践之余,也需要考虑自身因素。
首先是标准化层面。降低管理的复杂度有三种方法,即淘汰、标准化、模块化。对中国整车企业来说,标准化率仍有很大的提升空间。对于每一个具体的模块,可能并不仅仅是纯粹的模块化,而是几种方法的整合。
其次是关键资源控制层面。与国际汽车巨头相比,中国整车企业在传输、车轴、空调、后处理等关键系统方面的能力 和影响非常有限。通常,他们的专长集中在底盘、机身、发动机,而在其他关键系统方面十分依赖系统供应商。显然,有限的资源将影响模块化的范围和程度。为了 处理资源缺口,中国整车企业应根据业务战略,让重要供应商尽早参与到模块化战略中。
汽车企业在模块化战略上要取得成功,必须做好五方面工作。一是将模块化提上首席执行官优先议程,首席执行官需 定期关注应用在所有品牌和产品线的方法;二是高管层定期追踪和监管模块化的相关举措,确保项目实施;三是使所有模块化举措与产品规划同步,模块周期计划与 车辆周期计划必须一致;四是建立模块化与研发项目/产品研发工程师之间的联系,建立实施试点项目,在所有产品线进行推广;五是让模块供应商尽早参与。